如何識(shí)別自上料攪拌車底盤(pán)保護(hù)的優(yōu)缺點(diǎn)?
在潮濕和潮濕的條件下,您的水泥攪拌車底盤(pán)容易受到雨水侵蝕和生銹。大多數(shù)車主對(duì)自上料攪拌車底盤(pán)防護(hù)都有一定的了解,但是如何選擇水泥攪拌車底盤(pán)裝甲施工車間,如何識(shí)別施工質(zhì)量,是大多數(shù)車主非常關(guān)心的問(wèn)題。材料技術(shù)是水泥攪拌車底盤(pán)裝甲建設(shè)的關(guān)鍵。目前常用的水泥攪拌車底盤(pán)密封塑料加工一般只采用單柔性樹(shù)脂材料或?yàn)r青材料。3M水泥攪拌車底盤(pán)裝甲材料由四款性能獨(dú)特的產(chǎn)品組成。采用多層涂覆的方法,實(shí)現(xiàn)多種功能的保護(hù)。具有高附著力、高耐磨性、抗沖擊(高彈性)、耐腐蝕、耐噪音等綜合功能。
In wet and humid conditions, your cement mixer chassis is vulnerable to rain erosion and rust. Most car owners have a certain understanding of the chassis protection of self loading mixer, but how to select the armored construction workshop of cement mixer chassis and how to identify the construction quality are the issues that most car owners are very concerned about. Material technology is the key to the construction of cement mixer chassis armor. At present, the commonly used cement mixer chassis sealing plastic processing only uses single flexible resin material or asphalt material. 3M professional cement mixer chassis armor material is composed of four products with unique performance. Multi layer coating method is adopted to realize multi-function protection. With high adhesion, high wear resistance, impact resistance (high elasticity), corrosion resistance, noise resistance and other comprehensive functions.
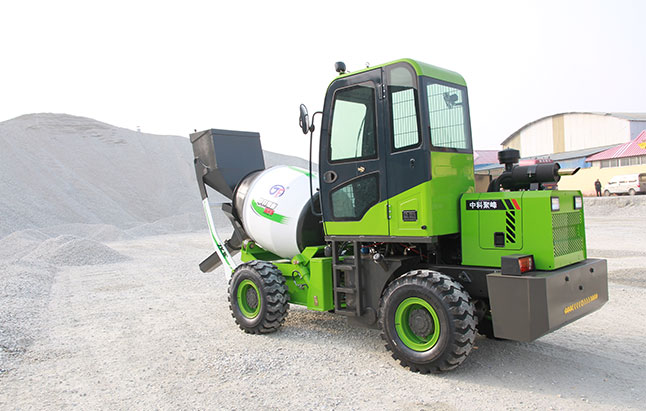
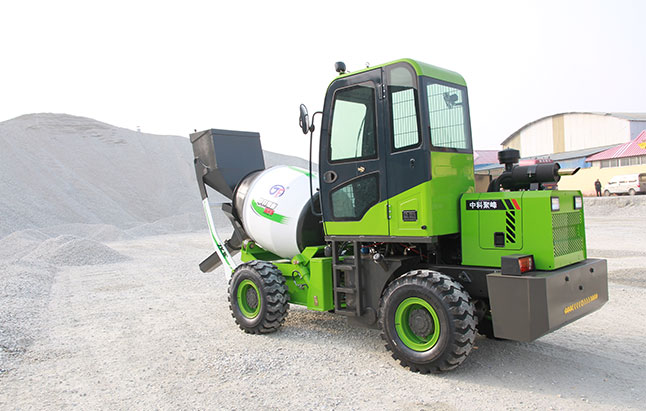
在施工上,自上料攪拌車底盤(pán)裝甲也有講究。無(wú)論新車還是舊車,必須全 面檢查水泥攪拌車底盤(pán)狀況,污垢、銹跡、油層;使用壓縮空氣吹干水泥攪拌車底盤(pán);做好車身蓋、蓋件:排氣管、制動(dòng)鼓、制動(dòng)器、減震器、油箱管路、發(fā)動(dòng)機(jī)底部、可拆卸螺栓、四輪驅(qū)動(dòng)后橋螺栓。然后開(kāi)始噴涂施工,說(shuō)到噴涂是關(guān)鍵的,噴槍噴嘴離水泥攪拌車底盤(pán)施工表面應(yīng)保持25厘米左右的距離,緩慢而均勻地移動(dòng),以保證噴涂層的均勻性。根據(jù)不同工藝的選擇,連續(xù)噴涂具有高吸附、高強(qiáng)度、高耐磨性的材料。整個(gè)水泥攪拌車底盤(pán)噴涂4 - 12次,每次干燥間隔15 - 30分鐘。噴藥后,下一步是移除障礙物并修復(fù)它。多功能混凝土攪拌車底盤(pán)裝甲建成后,可以提高駕駛性和舒適性,使混凝土攪拌車的綜合功能得到充分體現(xiàn)。
In the construction, the chassis armor of self loading mixer is also particular. Whether the new car or the old car, first of all, we must comprehensively check the condition of the cement mixer chassis, remove the dirt, rust and oil layer; use compressed air to dry the cement mixer chassis; do a good job in the body cover and cover parts: exhaust pipe, brake drum, brake, shock absorber, fuel tank pipeline, bottom of the engine, detachable bolts, four-wheel drive rear axle bolts. Then start spraying construction. When it comes to spraying, spraying is the key. The distance between the spray gun nozzle and the construction surface of cement mixer chassis should be about 25 cm, and move slowly and evenly to ensure the uniformity of spraying layer. According to the selection of different processes, continuous spraying of materials with high adsorption, high strength and high wear resistance. The whole cement mixer chassis is sprayed 4-12 times, and each drying interval is 15-30 minutes. After spraying, the next step is to remove the obstacle and repair it. After the construction of multifunctional concrete mixer chassis armor, the driving safety and comfort can be improved, and the comprehensive functions of concrete mixer can be fully reflected.